Reinigungsprozesse...
Grundsätzliches zur Prozessüberwachung ❗️
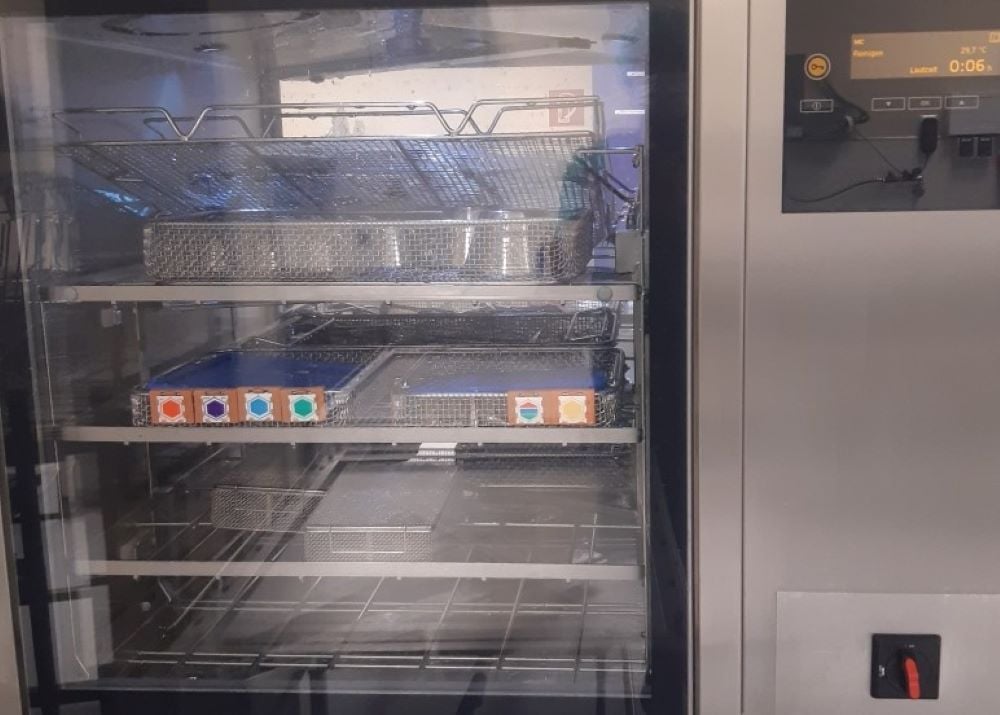
Hier haben wir nur eine kleine Auswahl von realen Prozessstörungen aus dem Alltag verschiedener Aufbereitungseinheiten:
Dosierfehler durch Luft im System
Dosierpumpe defekt
Enzyme durch Hitze geschädigt
Die meisten Reinigungsmittel am Markt enthalten Enzyme als reinigungsaktive Bestandteile. Enzyme sind Proteine, die bestimmte (Verschmutzungs-) Materialien hydrolisieren und damit abwaschbar machen können.
Enzyme sind hochwirksam, sie sind aber, wie alle Proteine, sehr wärmeempfindlich. Enzymhaltige Reinigungsmittel müssen deshalb stets bei niedrigen Temperaturen aufbewahrt werden, in der Regel wird als maximale Lagertemperatur 22°C angegeben. Schon bei leicht höheren Lagertemperaturen erreichen viele Reiniger bei weitem nicht mehr die Haltbarkeit, die laut Verfallsdatum angegeben ist.
Speziell in den Sommermonaten besteht die Gefahr, dass die Reiniger Temperaturen ausgesetzt werden, die die angegebenen Lagerbedingungen erheblich überschreiten, sowohl im Lager, als auch bei der Lieferung, siehe die nebenstehende Tabelle.
Wenn ein GKE-Reinigungsprozess-überwachungsindikator zur Chargenfreigabe verwendet und (vor allem im Sommerhalbjahr) das gewünschte Testergebnis plötzlich nicht mehr erreicht wird, dann fällt häufig auf, dass das Problem unmittelbar, nachdem ein neuer Kanister angeschlossen worden ist, auftritt.
Reinigungsmittel, die Enzyme enthalten und hitzegeschädigt werden, haben von Anfang an keine einwandfreie Reinigungswirkung. Dies kann vom RDG nicht bemerkt werden, ein „defekter“ Reiniger löst keinen Geräte-Alarm aus.
Diese Prozess-Störungen sind besonders ärgerlich, weil natürlich gerade bei einem neu angeschlossenen, ganz frischen Reinigungsmittel-Kanister von besonders guter Reinigungsleistung ausgegangen wird.
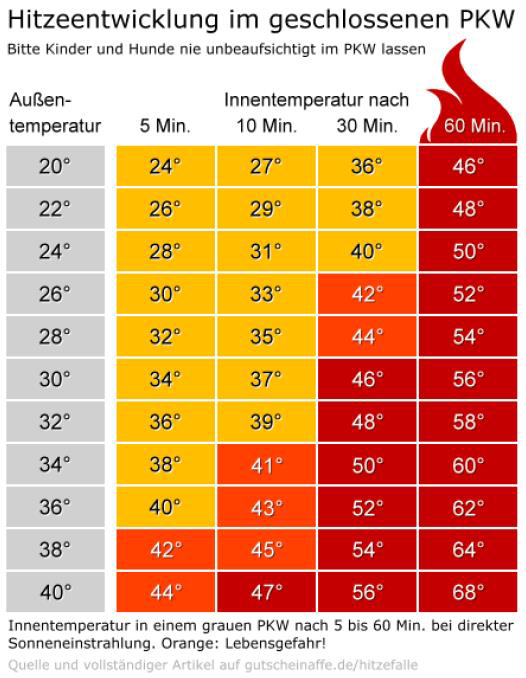
Falscher Reiniger wegen vertauschter Kanister
- Wenn ein alkalischer Reiniger verwendet wird, dann ist ein zweiter Kanister mit Neutralisator (Säure) angeschlossen, damit nach der Reinigung und vor der Schlussspülung wieder ein neutraler pH-Wert erreicht wird. Die beiden Kanister (Reiniger und Neutralisator) können vertauscht werden.
Wenn in einem Haus mehrere unterschiedliche Reinigungsmittel benutzt werden, dann können auch diese untereinander verwechselt werden. Zitat aus einer Kunden-E-Mail an GKE, nachdem der Indikator nicht mehr abgewaschen wurde: „wir haben den Fehler gefunden. Bei zwei Reinigungskanistern mit unterschiedlichen Inhaltsstoffen aber gleichem Aussehen, ist eine Verwechselung aufgetreten…“ - Wenn ein RDG chemisch desinfiziert (z. B. RDG für Endoskope), dann sind ein Reinigungs- und ein Desinfektionsmittel angeschlossen. Die beiden Kanister können vertauscht werden, ohne dass ein RDG Alarm auslöst. Zitat aus einem Zeitungsartikel im „Weser-Kurier“, einer Tageszeitung in Bremen, vom 05.02.2015: „Gut 300 Krankenakten werden […] derzeit überprüft, um auf Nummer sicher zu gehen. […] Offenbar waren an einer Maschine […] die Kanister für Reinigungsmittel mit denen für die Desinfektionslösung vertauscht worden.“
- Es gibt Reiniger, die in zwei Kanistern geliefert und erst im RDG zusammen gemischt werden. Der eine Kanister enthält eine alkalische Substanz, der andere Kanister eine Flüssigkeit mit reinigungsaktiven Enzymen. Zitat aus der E-Mail eines GKE-Außendienstmitarbeiters, der Testläufe mit Reinigungsprozessüberwachungsindikatoren bei einem Kunden begleitet hat: „Nach drei weiteren Durchgängen ist man auf Fehlersuche gegangen und stellte fest, dass an BEIDEN (!!!) Anschlüssen je ein Enzym-Kanister angeschlossen war! Nachdem man wieder den Reiniger angeschlossen hat, wurde nach 5-6 Durchgängen auch der Indikator wieder abgewaschen.“
Hygiene-Problem in einer Endoskopie - Weser-Kurier vom 05.02.2015
[Zitat]
Gut 300 Krankenakten werden am Klinikum Bremen-Nord derzeit überprüft, um auf Nummer sicher zu gehen. Anlass ist eine Unregelmäßigkeit bei der Aufbereitung medizinischer Endoskopie-Geräte, mit denen Ärzte die inneren Organe von Patienten begutachten. Offenbar waren an einer Maschine, die nach Behandlungen die Apparate wieder einsatzfähig macht, die Kanister für die Reinigungsmittel mit denen für die Desinfektionslösung vertauscht worden.
[/Zitat]
Der ganze Artikel: Weser-Kurier vom 05.02.2015